The blockage of anilox roller cells is actually the most unavoidable topic in the use of anilox rollers,Its manifestations are divided into two cases: the surface blockage of the anilox roller ( Figure. 1) and the blockage of the anilox roller cells ( Figure . 2).
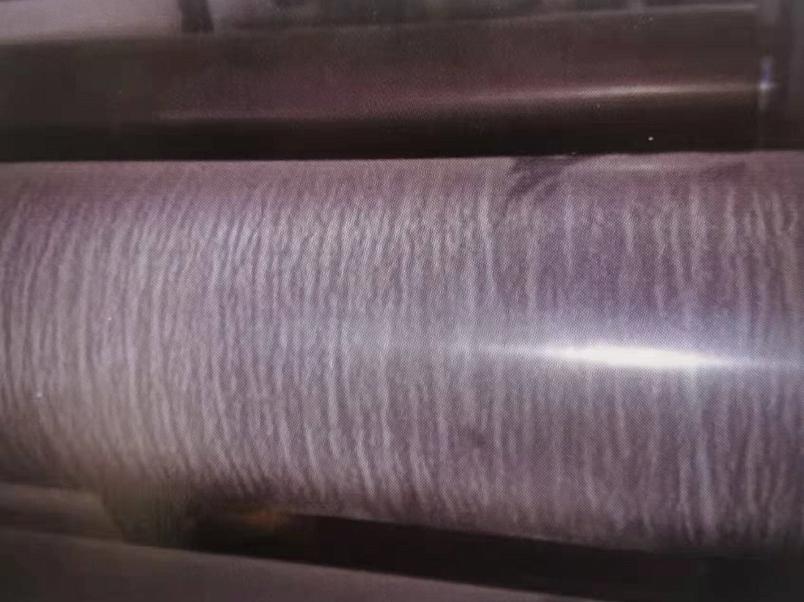
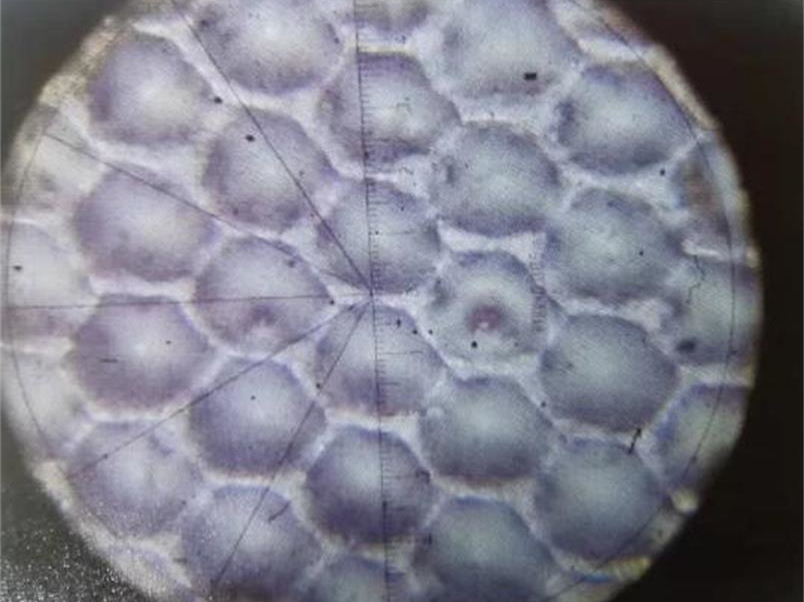
Figure .1
Figure .2
A typical flexo ink system consists of an ink chamber (closed ink feed system), anilox roller, plate cylinder and substrate, It is necessary to establish a stable transfer process of ink between the ink Chamber, anilox roller cells, the surface of the printing plate dots and the surface of the substrate in order to obtain high-quality prints. In this ink transfer path, the ink transfer rate from the anilox roll to the plate surface is approximately 40%, Ink transfer from plate to substrate is roughly 50%, It can be seen that such ink path transfer is not a simple physical transfer, but a complex process including ink transfer, ink drying, and ink redissolving; As the printing speed of the flexo printing machine is getting faster and faster, this complex process will not only become more and more complicated, but also the frequency of fluctuations in the ink path transmission will become faster and faster; The requirements for the physical properties of the holes are also getting higher and higher.
Polymers with a cross-linking mechanism are widely used in inks, such as polyurethane, acrylic resin, etc., to improve the adhesion, abrasion resistance, water resistance and chemical resistance of the ink layer. Since the ink transfer rate in the anilox roller cells is only 40% , That is to say, most of the ink in the cells is actually staying at the bottom of the cells during the entire printing process. Even if a part of the ink is replaced, it is easy to cause the ink to be completed in the cells. The resin cross-linking is done on the surface of the substrate, which leads to the blockage of the cells of the anilox roll.
It is easy to understand that the surface of the anilox roller is blocked. Generally, the anilox roller is improperly used, so that the ink is cured and cross-linked on the surface of the anilox roller, resulting in blockage.
For anilox roll manufacturers, the research and development of ceramic coating technology, the improvement of laser application technology, and the improvement of ceramic surface treatment technology after engraving of anilox rolls can reduce the clogging of anilox roll cells. At present, the commonly used methods are to reduce the width of the mesh wall, improve the smoothness of the inner wall of the mesh, and improve the compactness of the ceramic coating. .
For printing enterprises, the drying speed of the ink, the resolubility, and the distance from the squeegee point to the printing point can also be adjusted to reduce the blockage of the anilox roller cells.
Corrosion
Corrosion refers to the phenomenon of point-like protrusions on the surface of the anilox roller, as shown in Figure 3. Corrosion is caused by the cleaning agent infiltrating the bottom layer along the ceramic gap, corroding the bottom metal base roller, and breaking the ceramic layer from the inside, causing damage to the anilox roller (Figure 4, Figure 5).
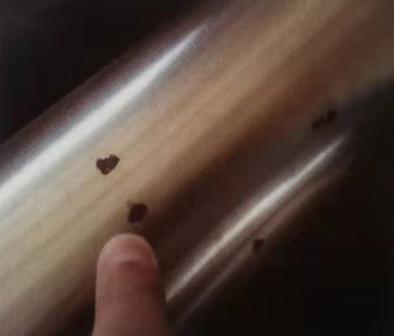
Figure 3
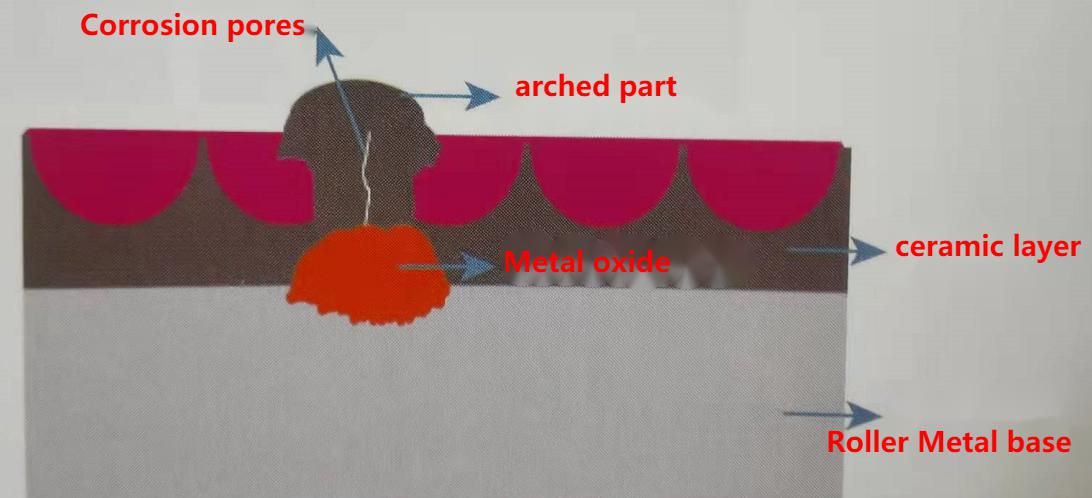
Figure 4
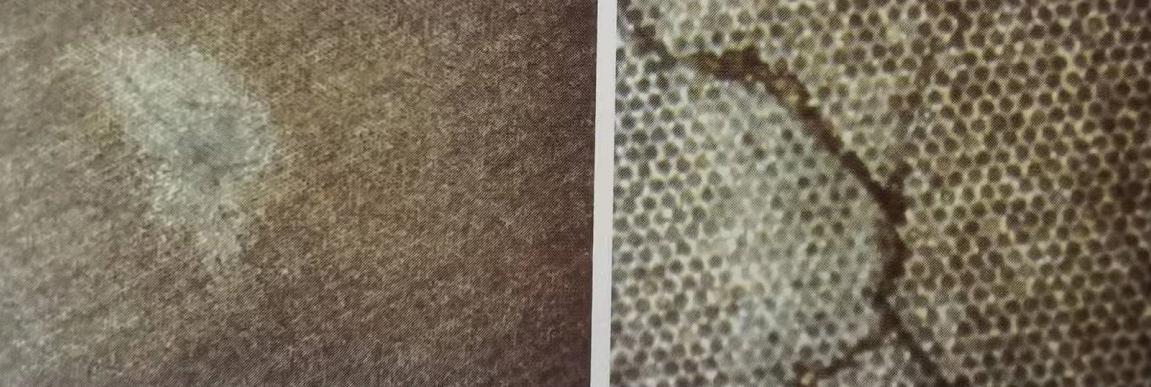
Figure 5 corrosion under the microscope
The reasons for the formation of corrosion are as follows:
① The pores of the coating are large, and the liquid can reach the base roller through the pores, causing corrosion of the base roller.
② Long-term use of cleaning agents such as strong acids and strong alkalis, without timely showering and air-drying after use.
③ The cleaning method is incorrect, especially in the equipment cleaning for a long time.
④ The storage method is incorrect, and it is stored in a humid environment for a long time.
⑤ The pH value of ink or additives is too high, especially water-based ink.
⑥ The anilox roller is impacted during the installation and disassembly process, resulting in the change of the ceramic layer gap.
The initial operation is often overlooked because of the long time between the onset of corrosion and the eventual damage to the anilox roll. Therefore, after finding the bagging phenomenon of the ceramic anilox roller, you should contact the ceramic anilox roller supplier in time to investigate the cause of the arch.
Circumferential scratches
Scratches of anilox rolls are the most common problems affecting the life of anilox rolls.(figure 6)It is because the particles between the anilox roller and the doctor blade, under the action of pressure, break the surface ceramics of the anilox roller, and open up all the mesh walls in the printing running direction to form a groove. The performance on the print is the appearance of darker lines.
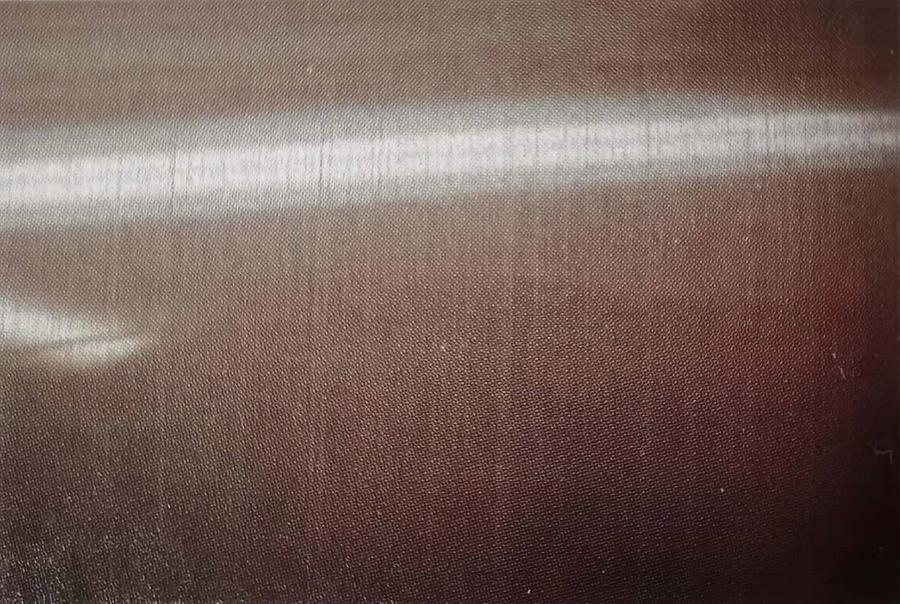
Figure 6 Anilox roll with scratches
The core problem of scratches is the change of the pressure between the doctor blade and the anilox roller, so that the original face-to-face pressure becomes the local point-to-face pressure; and the high printing speed causes the pressure to rise sharply, and the destructive power is amazing. (figure 7)
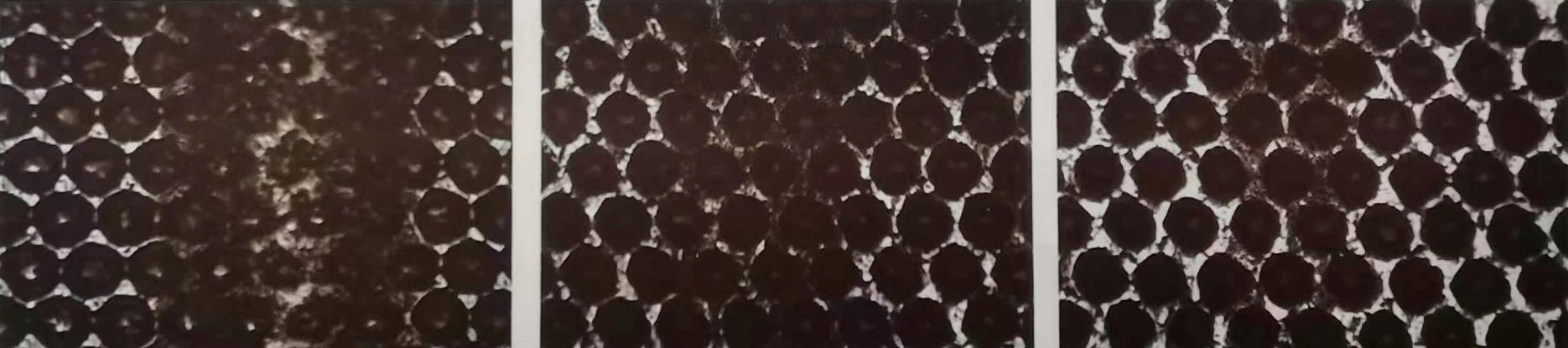
Figure 7 severe scratches
General scratches
minor scratches
Generally, depending on the printing speed, scratches that affect printing will be formed in 3 to 10 minutes. There are many factors that change this pressure, mainly from several aspects: the anilox roller itself, the cleaning and maintenance of the doctor blade system, the quality and installation and use of the doctor blade, and the design defects of the equipment.
1.the anilox roller itself
(1) The surface treatment of the ceramic anilox roller is not enough after engraving, and the surface is rough and easy to scratch the scraper and the blade of the scraper.
The contact surface with the anilox roller has changed, increasing the pressure, multiplying the pressure, and breaking the mesh in the state of high-speed operation.
The surface of the embossed roller forms scratches.
(2) A deep polishing line is formed during the polishing and fine grinding process. This situation generally exists when the anilox roll is delivered, and the lightly polished line does not affect the printing. In this case, the printing verification needs to be carried out on the machine.
2.the cleaning and maintenance of the doctor blade system
(1) Whether the level of the chamber doctor blade is corrected, a chamber doctor blade with poor level will cause uneven pressure. (figure 8)
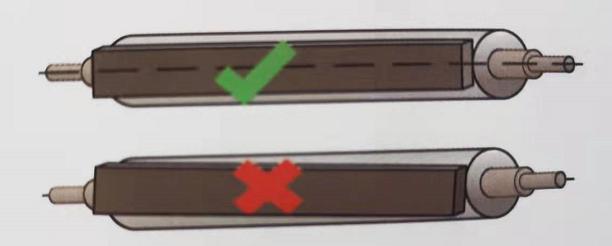
Figure 8
(2) Whether the doctor blade chamber is kept vertical, the non-vertical ink chamber will increase the contact surface of the blade. Seriously, it will directly cause damage to the anilox roller. Figure 9
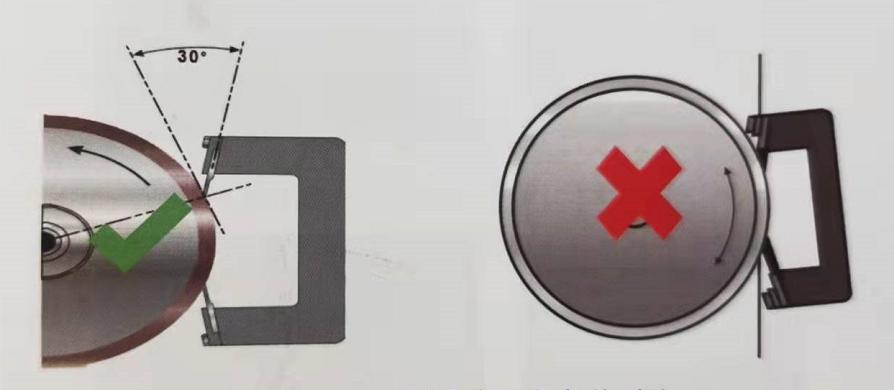
Figure 9
(3)chamber doctor blade system cleaning is very important, Prevent impurities from entering the ink system, stuck in between the doctor blade and the anilox roller. resulting in changes in pressure. Dry ink is also very dangerous.
3.The installation and use of the doctor blade
(1) Install the chamber doctor blade correctly to ensure that the blade is not damaged, the blade is straight without waves, and is perfectly combined with the blade holder, such as
As shown in Figure 10, make sure to keep the pressure even on the surface of the anilox roller.
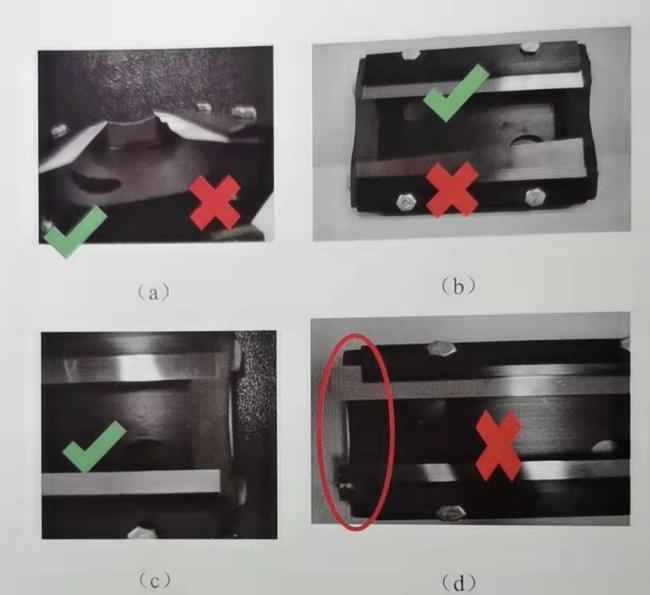
Figure 10
(2) Use high-quality scrapers. High-quality scraper steel has a tight molecular structure, as shown in Figure 11 (a), after wear The particles are small and uniform; the molecular structure of low-quality scraper steel is not tight enough, and the particles are large after wear, as shown in Figure 11 (b) shown.
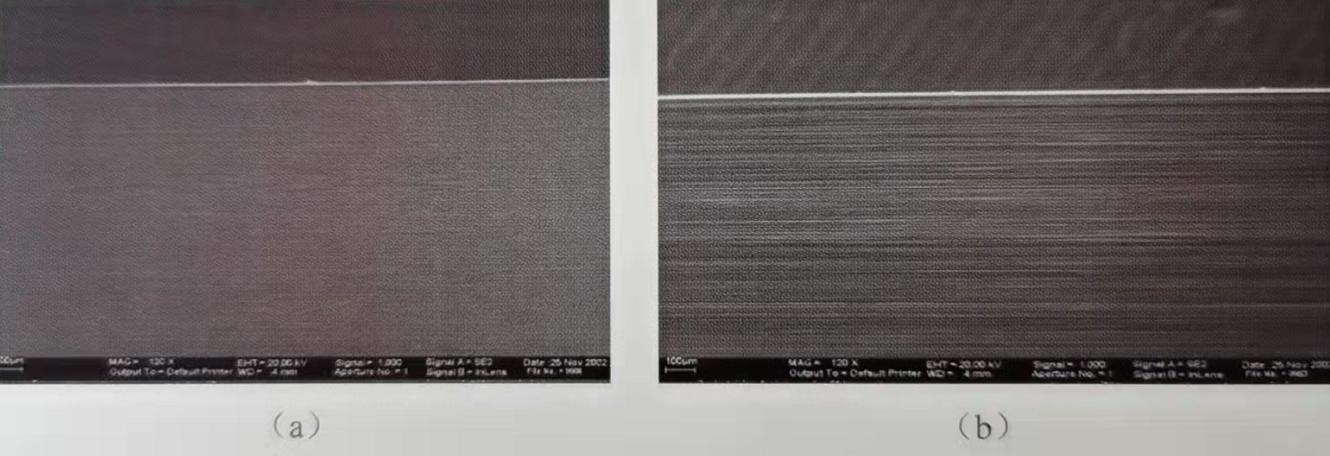
Figure 11
(3) Replace the blade knife in time. When replacing, pay attention to protect the knife edge from being bumped. When changing a different line number of the anilox roller, you must replace the blade knife. The wear degree of the anilox roller with different line numbers is inconsistent, as shown in Figure 12, the left picture is the low line number screen Grinding of the blade knife on the blade knife The condition of the damaged end face, the picture on the right shows the condition of the worn end face of the high line count anilox roller to the blade knife. The contact surface between the doctor blade and the anilox roller with mismatched wear levels changes, causing pressure changes and scratches.
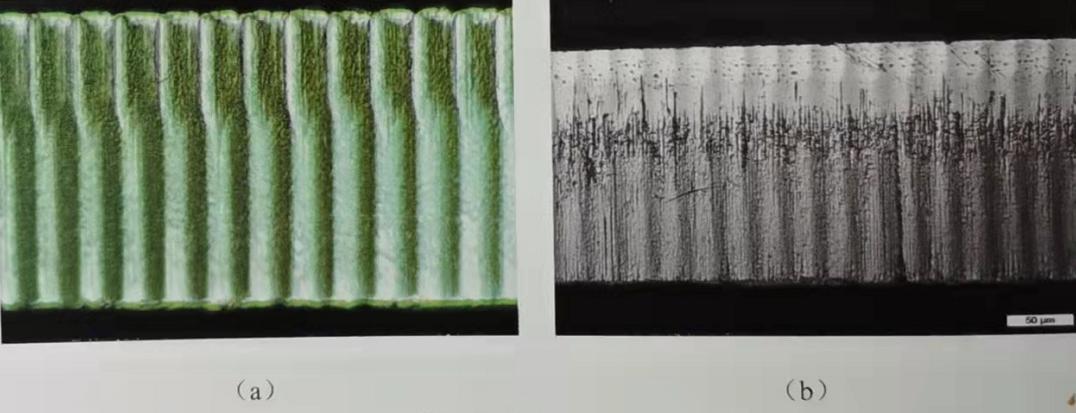
Figure 12
(4) The pressure of the squeegee should be light, and the excessive pressure of the squeegee will change the contact area and angle of the squeegee and the anilox roller, as shown in Figure 13. It is easy to entrain impurities, and the entrained impurities will cause scratches after changing the pressure. When unreasonable pressure is used, there will be worn metal tails on the cross section of the replaced scraper Figure 14. Once it falls off, it gets caught between the scraper and the anilox roller, which may cause scratches on the anilox roller.
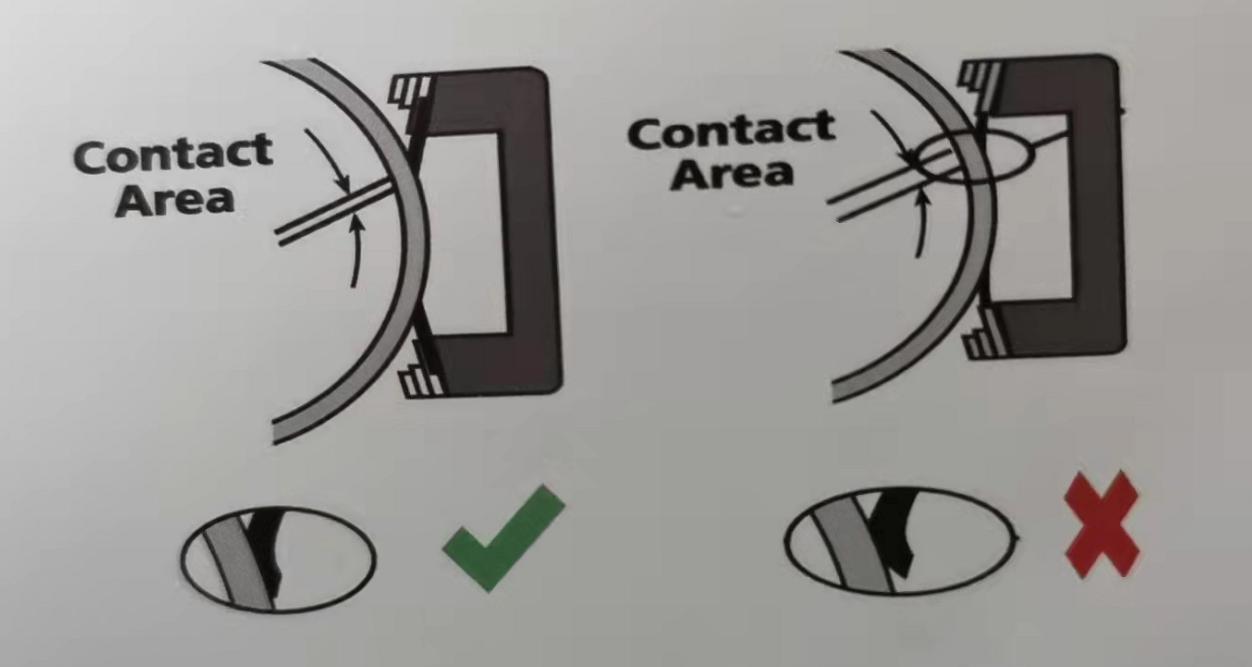
Figure 13
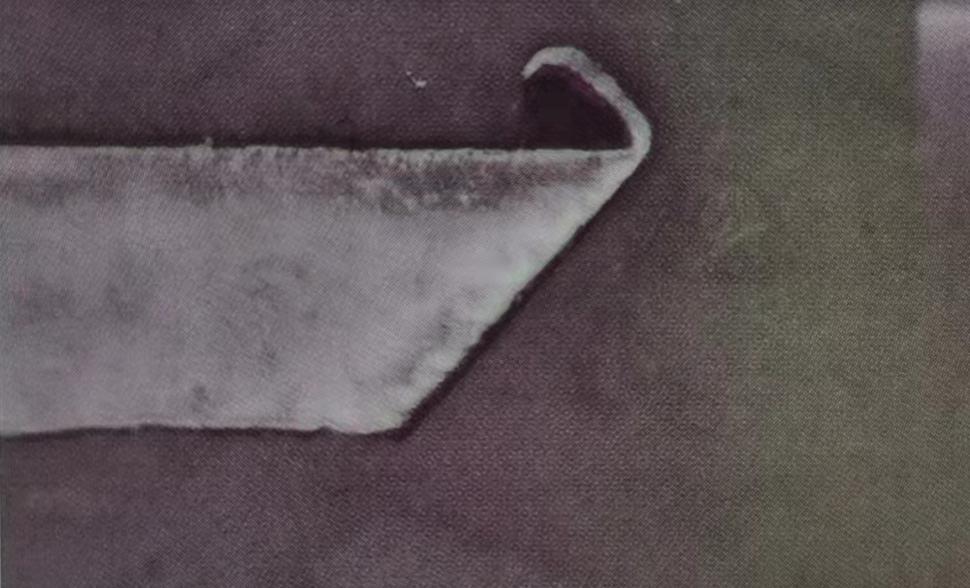
Figure 14
4.the design defects of the equipment
Design flaws can also cause scratches to occur easily, such as a mismatch between the design of the ink block and the diameter of the anilox roll. The unreasonable design of the squeegee angle, the incongruity between the diameter and length of the anilox roller, etc., will bring uncertain factors. It can be seen that the problem of scratches in the circumferential direction of the anilox roll is very complicated. Paying attention to changes in pressure, cleaning and maintenance on time, choosing the right scraper, and good and orderly operating habits can greatly alleviate the scratch problem.
Collision
Although the hardness of ceramics is high, they are brittle materials. Under the impact of external force, the ceramics are easy to fall off and produce pits (Figure 15). Generally, bumps occur when loading and unloading anilox rollers, or metal tools fall off the roller surface. Try to keep the printing environment clean, and avoid stacking small parts around the printing press, especially near the ink tray and anilox roller. It is recommended to do a good job of anilox. Proper protection of the roller to prevent small objects from falling and colliding with the anilox roller. When loading and unloading the anilox roller, it is recommended to wrap it with a flexible protective cover before operation.
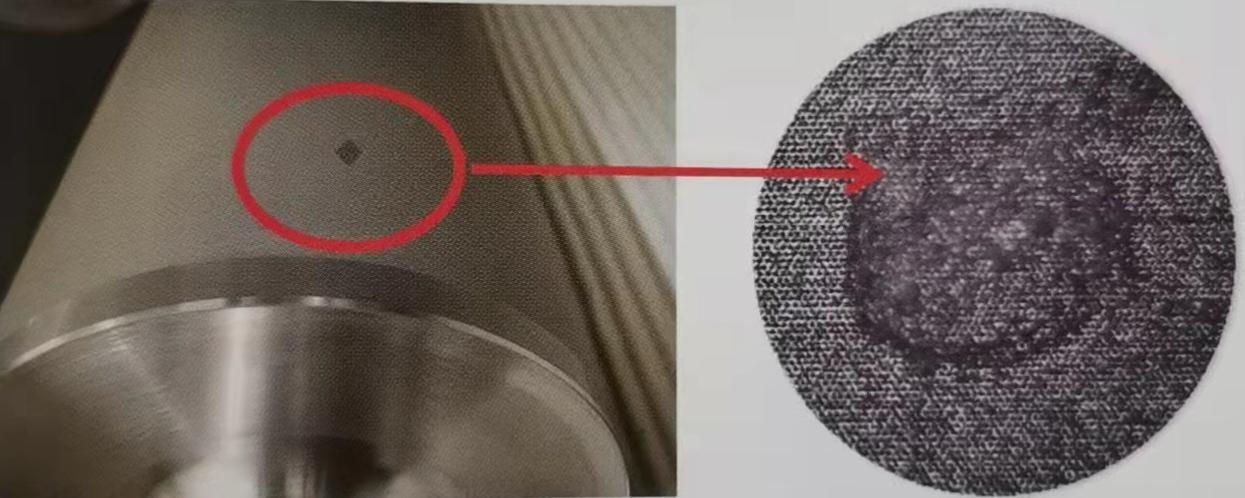
Figure 15
Post time: Feb-23-2022