The daily maintenance of the a gearless flexo printing press needs to focus on cleaning protection and system maintenance.As a precision equipment, the cleaning and maintenance of the flexographic printing machine needs to be carried out throughout every production link. After stopping, the ink residue of the printing unit, especially the anilox roller, plate roller and scraper system, must be removed immediately to avoid dry blockage and affect the uniformity of ink transfer.
When cleaning, special cleaning agents and soft cloth should be used to gently wipe the anilox roller mesh holes to prevent hard objects from damaging its delicate structure. Dust removal on the surface of the machine body, guide rails and servo motor heat dissipation ports is also critical to ensure smooth heat dissipation and stable mechanical movement. Lubrication maintenance must strictly follow the equipment specifications, and regularly add specified grease to guide rails, bearings and other components to reduce friction loss and maintain the long-term accuracy of the flexographic printing machine. In addition, daily inspections of the sealing of pneumatic pipelines and dust accumulation in electrical cabinets can effectively prevent sudden failures.
The system stability of the flexographic printing machine depends on the dual maintenance of hardware and software. Although the gearless transmission structure simplifies the mechanical complexity, it is still necessary to regularly check the tightness of the servo motor and the tension of the synchronous belt to avoid looseness and registration deviation. In terms of the control system, it is necessary to monitor the servo drive parameters in real time and calibrate the registration system . The sensitivity of the tension sensor and the vacuum adsorption device directly affects the material transmission, and daily cleaning and functional testing are essential. In long-term use, the consumables management of the flexographic printer is equally important, such as timely replacement of scraper blades and aging ink tubes, and regular backup of equipment parameters to deal with data anomalies. Temperature and humidity control of the workshop environment can reduce material deformation and electrostatic interference, and further optimize the printing effect. Only through scientific and systematic maintenance strategies can flexographic printing presses continue to exert their advantages of high precision and high efficiency, while sustaining efforts to facilitate structural optimization and technological advancement within the print-packaging industrial ecosystem.
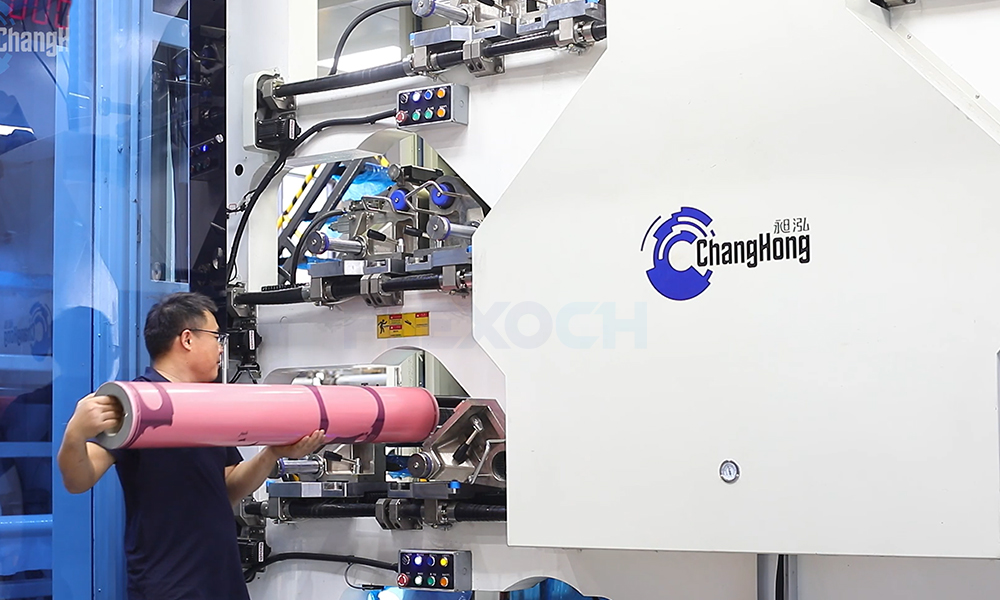
Gearless flexo printing press details display
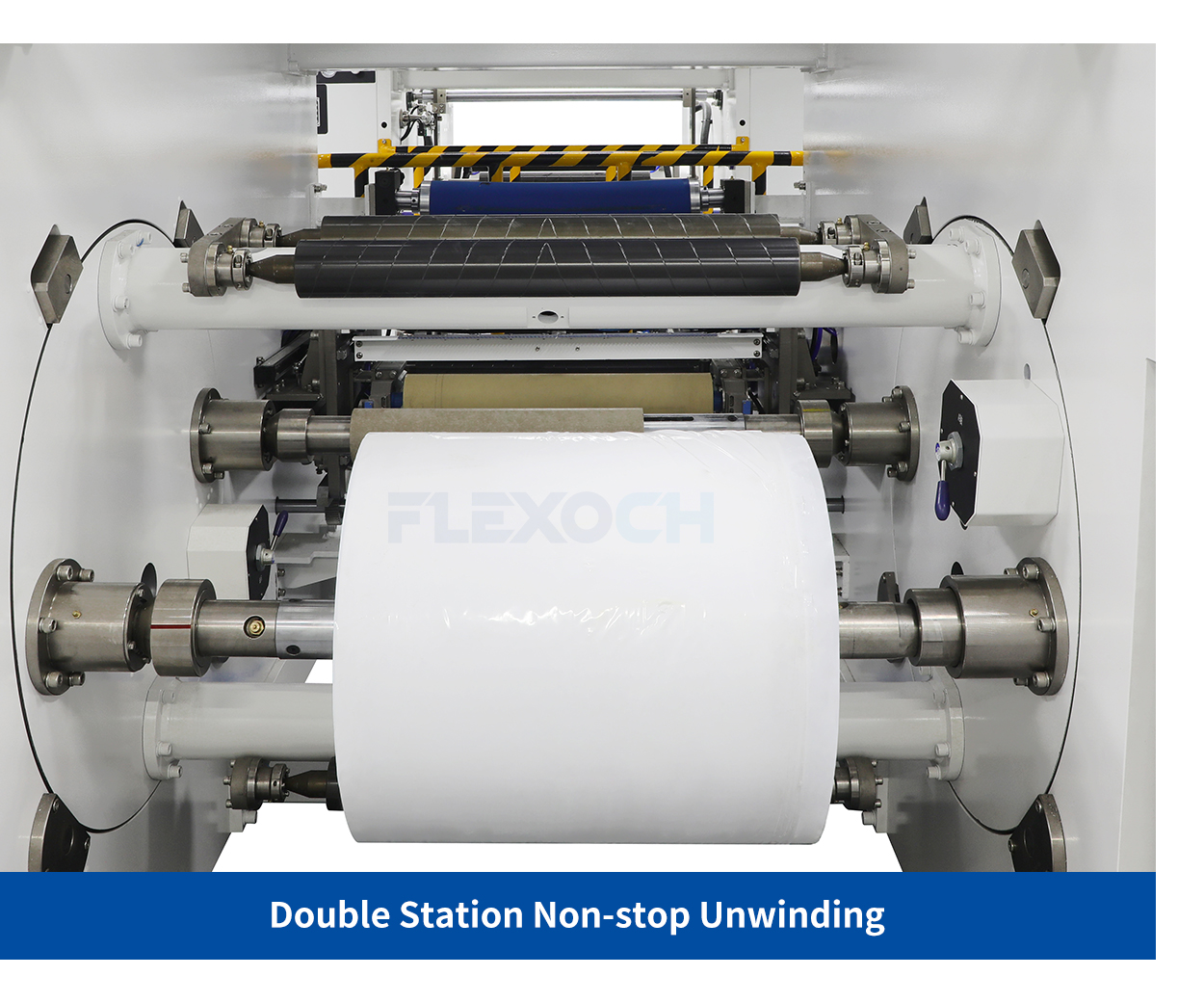
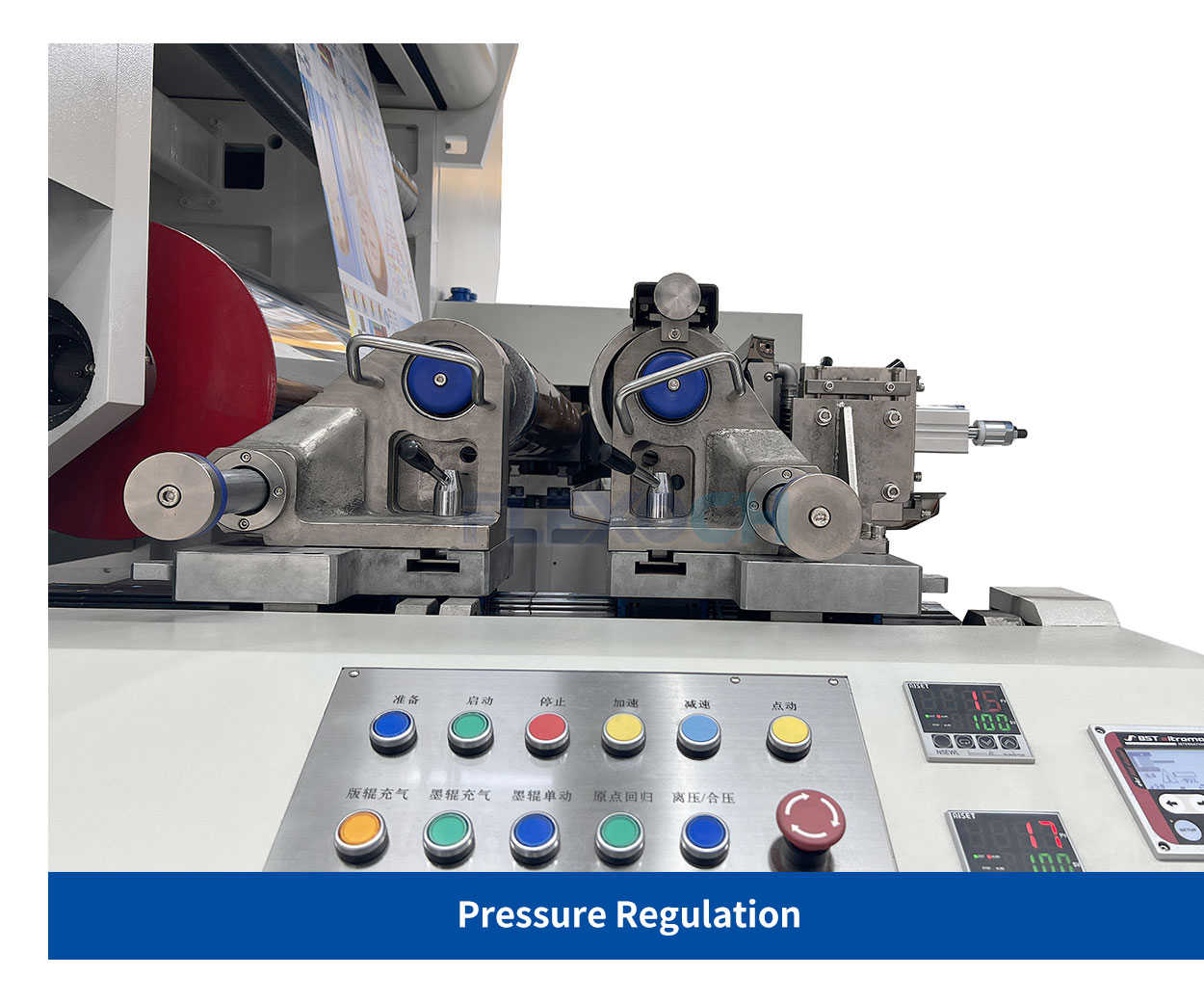
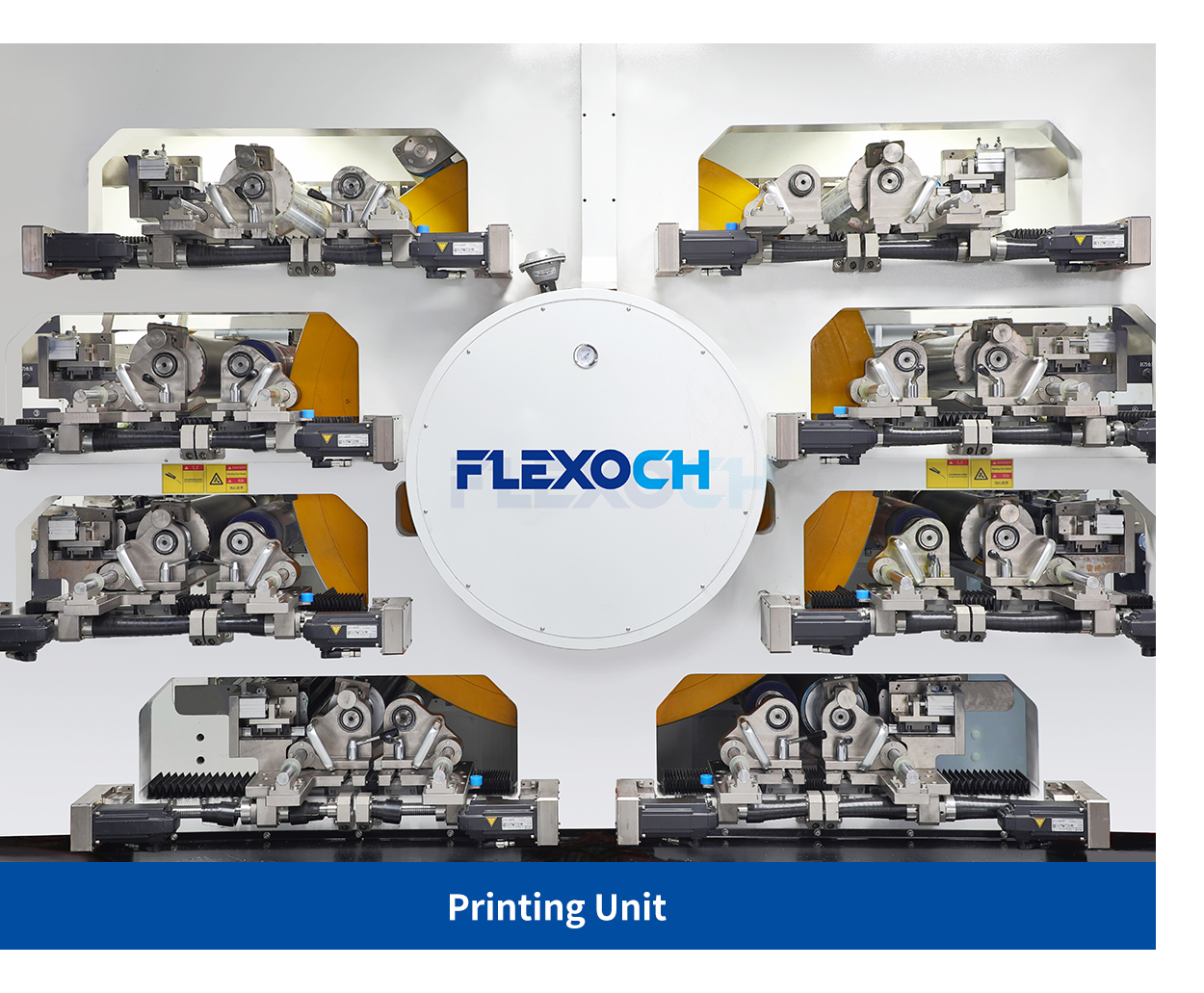
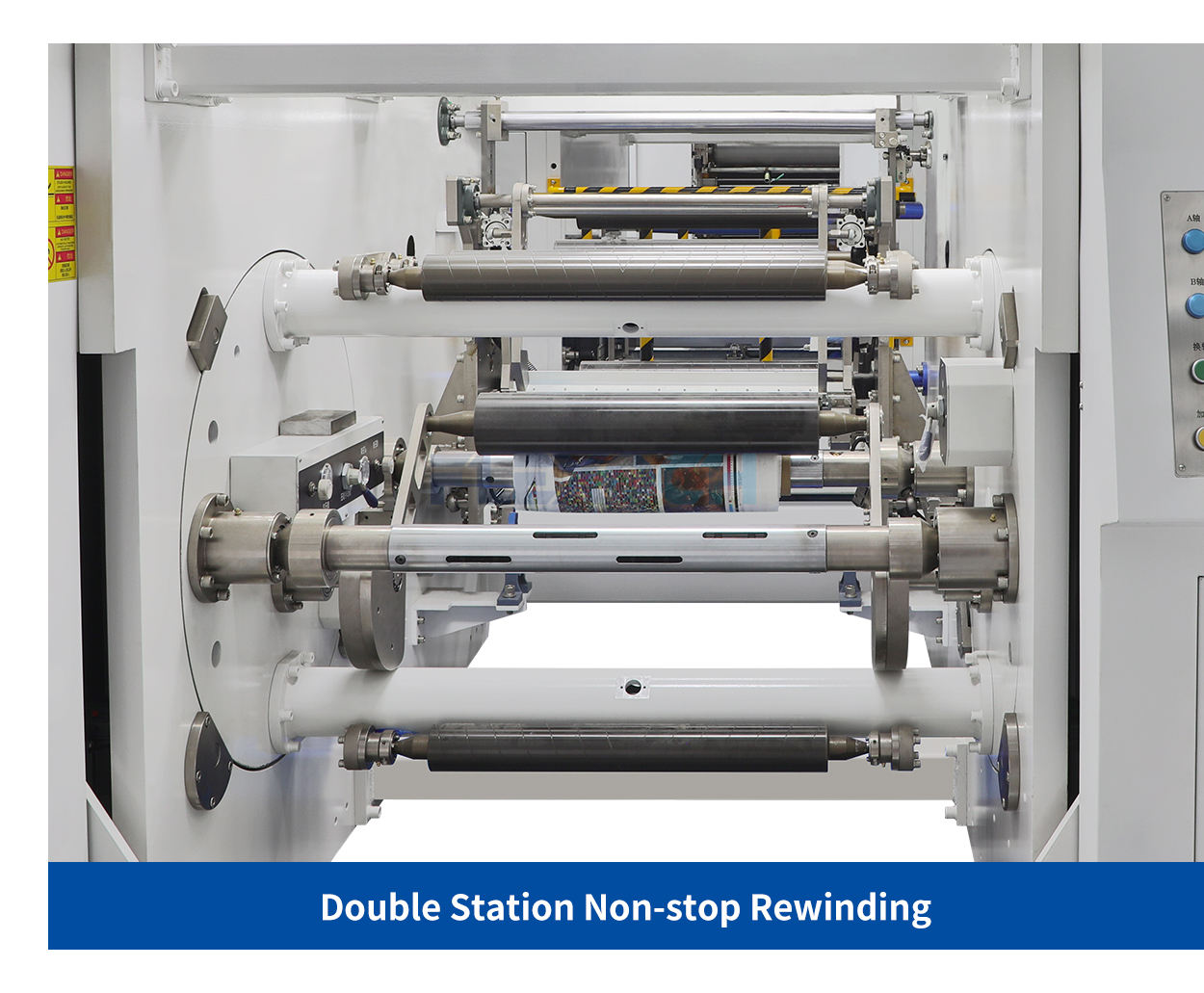
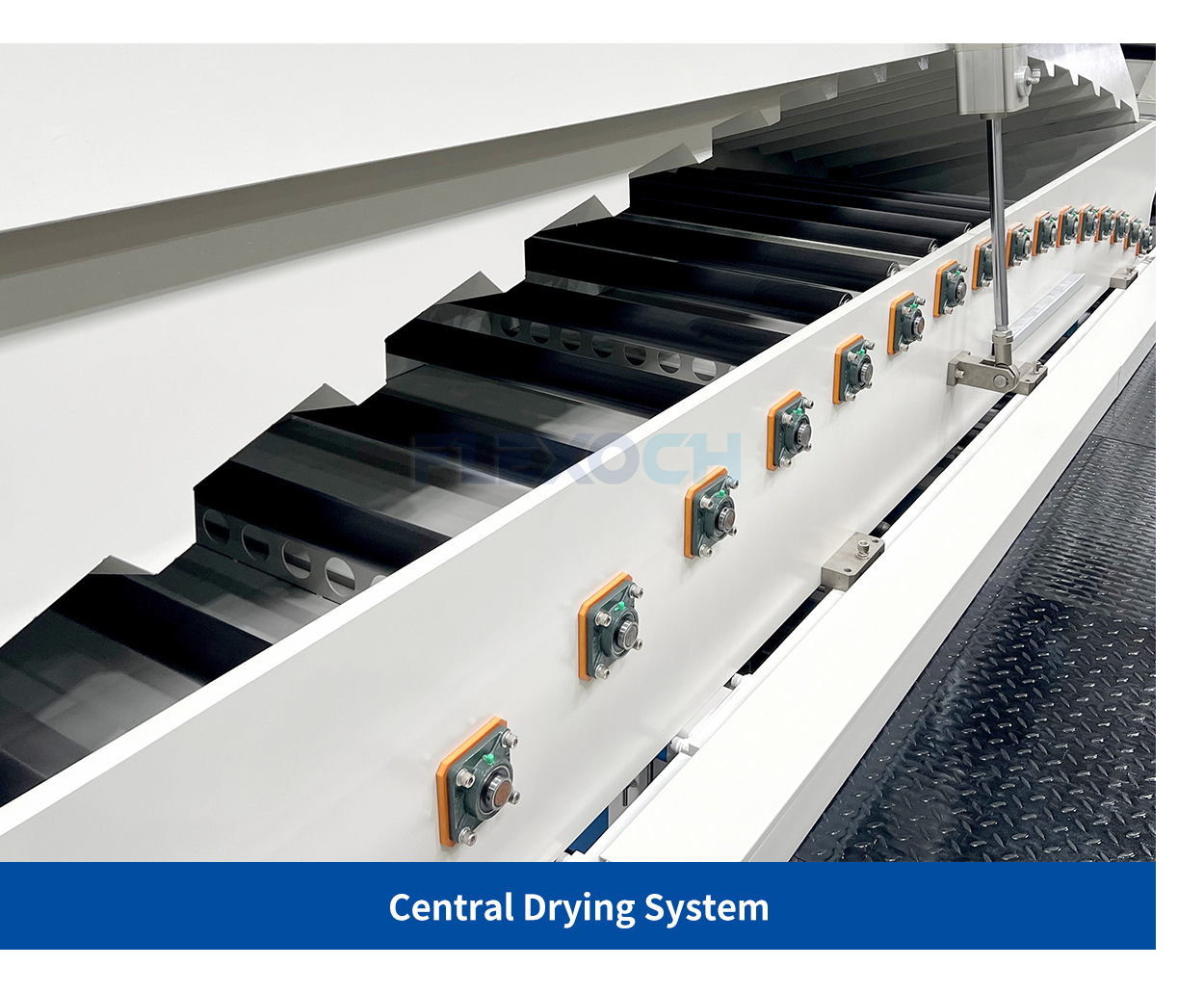
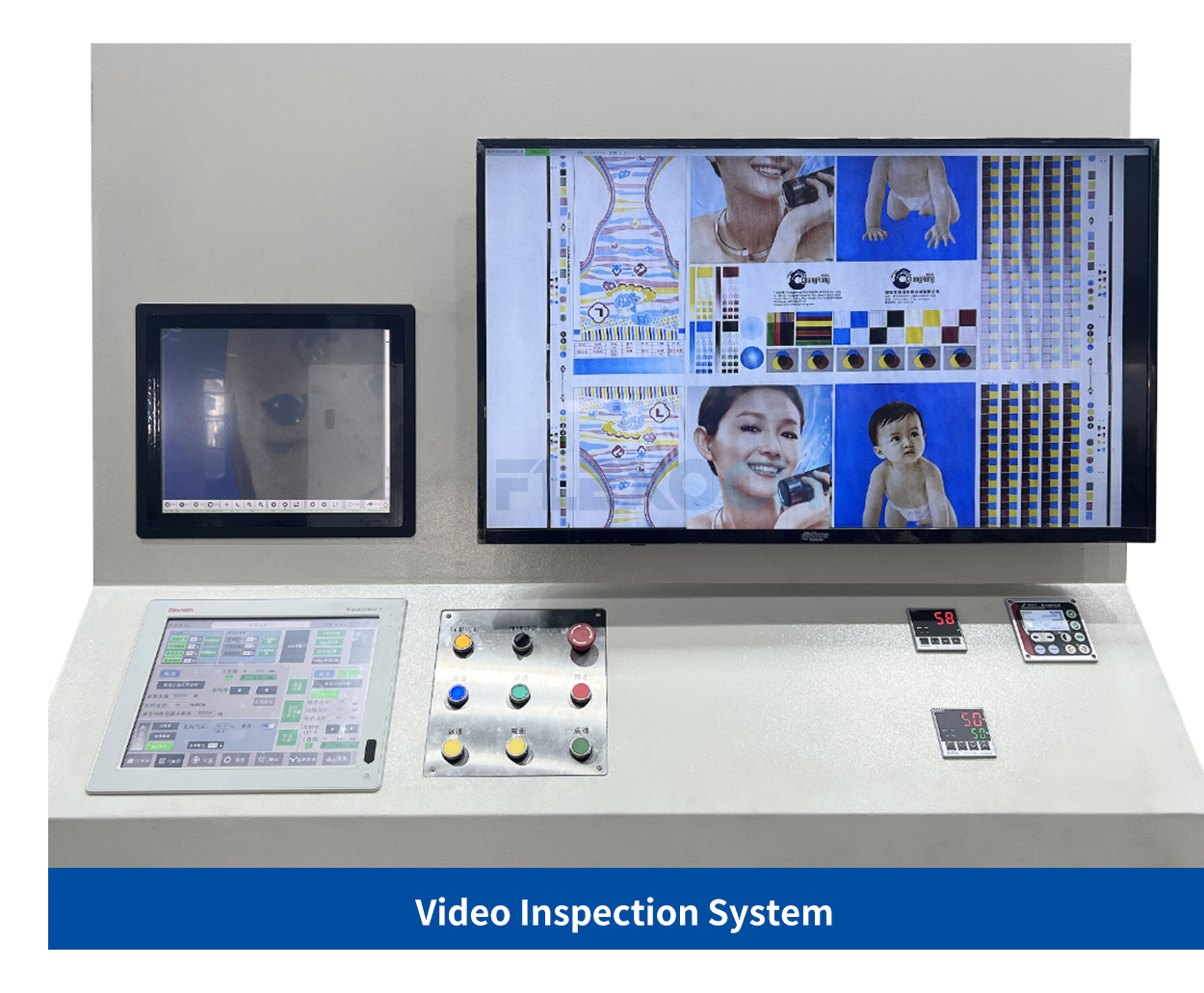
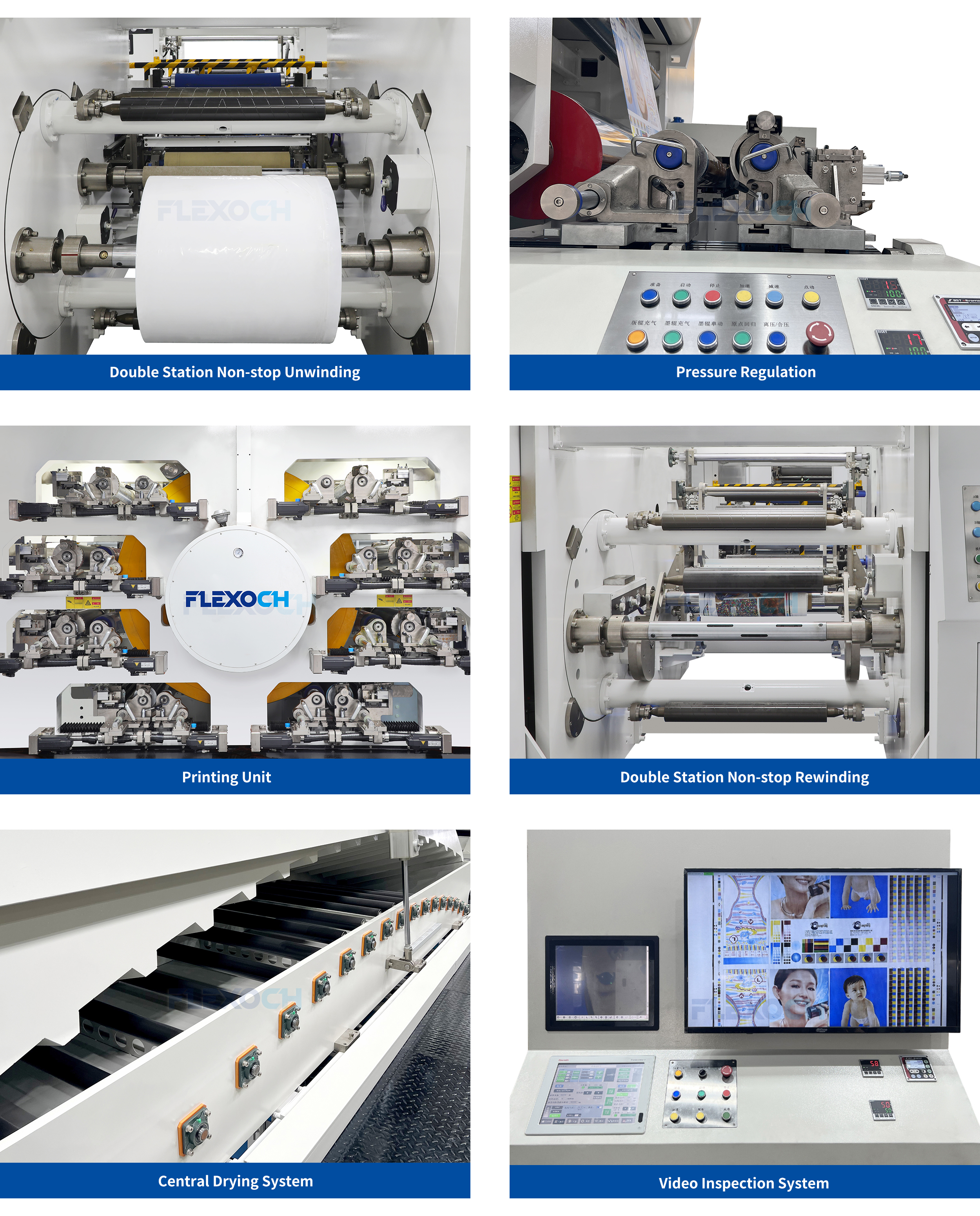
Post time: Apr-11-2025